Электроэрозионная обработка металла
Электроэрозионная обработка (CNC Wire Cut EDM Machine) металлов, сплавов, деталей,
узлов, инструментов.
Предоставляет полный комплекс услуг для производства и обработки готового изделия, а так же выполняем заказы по
электроэрозионной резке металла.
Наше оборудование позволяет выполнять электроэрозионную обработку токопроводящих материалов и
изготавливать детали различной формы и сложности.
- обработка стали любой твердости;
- обработка титана;
- твердых сплавов;
- жаропрочных сплавов;
- обработка магнитов;
- прошивка отверстий, полостей, углублений;
- получение методом копирования профилированных поверхностей, отверстий любого сечения;
- нанесение надписей и маркировки на металлах;
- изготовление прототипов статоров электродвигателей из магнитной стали;
- изготовление планетарных редукторов.
Электроэрозионная обработка на проволочных вырезных станках с ЧПУ |
Размер рабочего стола (Д x Ш), мм |
415 х 635 |
Перемещение рабочего стола (X x Y), мм |
320 х 400 |
Максимальная высота реза, мм |
300 |
Возможный угол наклона проволоки, ° |
±30 |
Максимальный вес заготовки, кг |
100 |
Стоимость электроэрозионной обработки металла |
500 руб. нормо-час * |
* - При больших объёмах реза или низкой точности - цена договорная
ПРИМЕРЫ НАШИХ РАБОТ
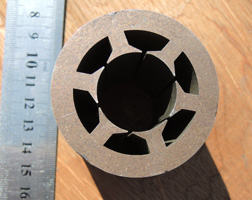 |
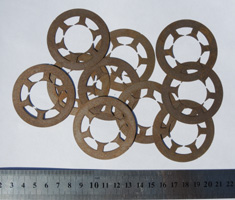 |
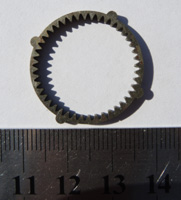 |
Статор электродвигателя из магнитной стали |
Шестерня планетарного редуктора с внутренним зацеплением |
Электроэрозионная обработка
Автор: Евгений Дряхлов
Сущностью процесса электроэрозионной резки является воздействие на деталь искровых разрядов,
образующихся вследствие протекания импульсного тока с частотой в районе 240 кГц между электродом-проволокой и
деталью, находящихся в непосредственной близости друг от друга в среде жидкого диэлектрика. В результате этих
разрядов из материала детали выбиваются микрочастицы, которые выносятся из межэлектродного зазора (GAP) струей
диэлектрика. Кроме этого, диэлектрик играет роль катализатора процесса распада, так как при высочайшей
температуре разряда диэлектрик в зоне эрозии превращается в пар. Происходит дополнительный микровзрыв пара,
который не может сразу выйти из межэлектродного зазора.
За последние годы электроэрозионная обработка не только окончательно закрепила свои позиции в современном
инструментальном производстве, но и продолжает развиваться быстрыми темпами в направлении улучшения
качественных показателей и предложения новых конструктивных решений.
Открытие формообразующего воздействия электрической эрозии на токопроводящие материалы состоялось в 1943
году и принадлежит нашим соотечественникам - супругам Б. и Н. Лазаренко. Когда повсюду в мире в 50-х годах
лучшие умы всерьез взялись за эту технологию, чья-то советская руководящая воля свернула перспективные
разработки и ввергла нас в отставание на многие десятки лет в области электроэрозионной обработки. Ну что
же, как это не горько, поговорим об успехах других.
Диэлектрик в электроэрозионной обработке
Советские исследователи, супруги Лазаренко, которые впервые и открыли возможность использования
явления электрической эрозии для обработки токопроводящих материалов, в качестве диэлектрика вначале
использовали окружающий воздух. Однако скоро выяснилось, что производные минеральных масел имеют в этом плане
несравнимые преимущества: сила разряда - больше, можно
работать с меньшими искровыми промежутками, что улучшает точность операции. Новый материал диэлектрика также
позволил увеличить частоту разрядов и лучше вымывать частички эродированного металла.
С 1960 года на рынок стали выходить химические компании, предлагающие специальные составы для использования
в электроэрозионных установках.
О сути процесса:
Электроды - инструмент и заготовка - закреплены оснасткой станка и не соприкасаются друг с другом.
Генератор электрических импульсов задает периодичность и напряженность электрического поля вокруг электродов. Во
время процесса электроискрового воздействия серия периодических блуждающих электрических разрядов снимает
тончайший слой материала с заготовки.
В точке, где напряженность электрического поля достигает максимума, происходит электрический разряд -
молния в "микроатюре". Под действием электрического поля электроны и свободные положительные ионы разгоняются
до высоких скоростей и моментально образуют ионизационный туннель, обладающий электрической проводимостью.
Возникает электроток, и между электродом и заготовкой образуется искровой разряд, приводящий к
столкновениям элементарных частиц. Во время этого процесса образуется газовый пузырек, давление которого непрерывно
нарастает до образования плазменной зоны. Плазменная зона быстро достигает сверхвысоких температур -
от 8000 до 12000°С - благодаря нарастающему числу столкновений элементарных частиц. Этот процесс приводит к
моментальному плавлению микрослоев вещества у электрода. При исчезновении электрического поля внезапное снижение
температуры приводит к взрыву плазменного пузырька, что сопровождается отрывом части материала с заготовки,
и к образованию на этом месте микроскопического кратера. Эродированный материал затем формируется заново в виде
маленьких сфер, которые вымываются жидкостью-диэлектриком. При очень коротком разрядном импульсе в движение
приводится больше отрицательно заряженных частиц, нежели положительно заряженных. Чем больше частиц определенного
заряда движутся к электроду, тем больше тепла вырабатывается на его поверхности. Из-за большего размера положительные
частицы способствуют выработке большего тепла при тех же скоростях бомбардировки электрода-цели. Чтобы
минимизировать снятие материала заготовки или износ инструмента, полярность выбирается таким образом, чтобы как
можно больше тепла высвобождалось со стороны заготовки до завершения разряда. Для чего при коротких разрядах
электрод-инструмент соединяется с отрицательной клеммой и, таким образом, имеет отрицательную полярность.
При длительных разрядах, наоборот, электрод-инструмент подключается к положительному полюсу. На протяженность
импульса, при которой должна поменяться полярность на заготовке и электроде-инструменте. влияет целый ряд
факторов, в большей степени зависящих от физических параметров инструмента и свойств материала электрода.
Когда идет обработка стали медным электродом, продолжительность периодичного генерируемого импульса составляет
порядка 8 микросекунд.
Неблизнецы-братья
Технология электроэрозионной обработки продолжает развиваться по двум основным направлениям: проволочная
электроэрозионная резка (wire electric discharge machining) и копировально-прошивная электроэрозионная
обработка (ram (die sinking) electric discharge machining).
Проволочная электроэрозионная резка
Проволочная резка начала свое развитие с чистого листа в начале 70-х годов. Глобальное совершенствование
процесса пришлось на период с середины 80-х до середины 90-х годов. Прогресс обозначился по шести ключевым
направлениям известного соотношения цена-качество:
скорость обработки;
размер заготовки;
угол конусной резки;
цена;
точность;
длительная работа без вмешательства человека.
Функции диэлектрика:
Электроизолирующая. Диэлектрик должен разделять заготовку и электрод. Искровой разряд
должен происходить в максимально узком промежутке между заготовкой и электродом, что позволяет сделать
процесс производительным и точным.
Ионизационная. За очень короткое время необходимо создать все условия для формирования электрического
поля. После импульса зона разряда должна быть очень быстро деионизирована для возможности повторного
разряда. Диэлектрик должен способствовать максимальному сужению искровой зоны, чтобы добиться высокой
плотности энергии в этой зоне.
Охлаждающая. Искровой разряд имеет сверхвысокую температуру, поэтому диэлектрик должен остудить и
электрод, и заготовку. Также важно увести металлические газы, образующиеся в процессе электроэрозии.
Промывочная. Чтобы избежать электрического пробоя диэлектрик должен эффективно удалять эродированные крупицы металла.
Скорость. Номинальная максимальная скорость резки на сегодняшний день превышает 300 кв. мм/мин, (в лабораторных
условиях реализована скорость вырезки 600 кв. мм/мин.). Конечно, средняя скорость резки в реальных
производственных условиях ниже номинальных величин, однако и это впечатляет по сравнению с показателями
четвертьвековой давности (25-30 кв. мм/мин.). Появление новых сплавов для проволоки может отодвинуть и эти рубежи.
Размер заготовки. Максимальные размеры заготовок, пригодных для обработки на вырезных станках, по осям Х и V
достигают метра и даже больше (1300-1380 мм - по оси X). Однако особенно сильно за последние десятилетия
вырос габаритный размер заготовки по оси 2, который сейчас доходит до 400 мм. До этой же отметки поднялись
и координатные перемещения по оси 2. Всего этого удалось добиться благодаря новым конструктивным решениям,
объединившим принципы неподвижности заготовки и более точной и жесткой реализации осевых движений.
Угол конусной резки. В современных установках достигаются углы вырезки конических отверстий до 30 градусов
для заготовок толщиной до 400 мм. Более того, некоторые фирмы в качестве опциона предлагают установки с
возможностью достижения конусности до 45 градусов. Такие возможности позволили с начала 90-х годов значительно
расширить область применения электроэрозионной резки. Так, если раньше головки для экструзионных установок
собирались из набора отдельно обработанных тонких пластин, то новые возможности электроэрозионных станков
позволили изготавливать экструзионные головки из одной заготовки и за одну операцию. За счет этого
удалось значительно снизить объем скрапа и увеличить производительность экструзионного процесса.
Цена. За более чем четверть века непрерывных работ на порядок улучшились характеристики вырезных станков, в
то время как за этот же период оборудование подешевело приблизительно на 75% (с учетом фактора инфляции). Целый
ряд обстоятельств способствовал снижению цены. Электронная начинка оборудования вобрала много решений, пришедших
из компьютерной индустрии, которые уже тогда отличались прекрасным соотношением цена-качество - возросшая
вычислительная мощь за меньшие деньги. Сильно увеличился объем производства электроэрозионного оборудования, что
повысило эффективность таких производств. Кроме того, все новые и новые технические решения также способствовали
планомерному снижению цен на установки.
Точность. Еще в 70-х и начале 80-х годов оператору станка приходилось вначале делать пробный рез образца и затем
корректировать первоначальные настройки, прежде чем выйти на точные геометрические размеры изделия.
Искровые промежутки
Искровой промежуток разделяет заготовку и электрод. Даже при малой глубине обработки
различают два типа промежутка: фронтальный и боковой. Фронтальный задается системой управления, в то время
как боковой искровой промежуток зависит от продолжительности и высоты разрядного импульса, сочетания
материалов, напряжения холостого хода и других заданных параметров.
Блок питания является важнейшим элементом электроэрозионной установки. Он преобразует переменный ток из
силовой сети в прямоугольные импульсы определенной полярности. Размер импульсов и интервал между ними
задается системой управления в соответствии с выполняемым режимом обработки. Сила тока разряда пропорциональна
высоте импульса. Интервал между импульсами соответствует моменту отсутствия искрового разряда, а протяженность
импульса соответствует длительности искрового разряда. Обе эти величины составляют тысячные или даже
миллионные доли секунды.
Интервал между отдельными импульсами (длительность отсутствия электрического тока) также задается системой
управления. Интервал измеряется в процентном отношении собственной длительности к длительности импульса.
Теперь все эти мытарства остались в прошлом и сегодняшняя точность станков достигает 0,001 мм.
Вовлечение современных информационных технологий (САD/САМ - системы) в технологический процесс также
позволило увеличить точность обработки - новые установки со всем комплексом современного оснащения гарантировали
повторение заложенной в программе геометрии с большой степенью точности.
Как уже отмечалось, современные модели станков на 75% дешевле своих ранних предшественников, в то же самое
время они в 3-5 раз точнее.
Длительная работа без вмешательства человека. В 70-х годах электроэрозионные установки могли работать целыми
часами без вмешательства оператора - тогда скорости резки были слишком малыми. В современных
условиях, когда значительно возросли скорости обработки, практически полностью безлюдное производство
обеспечивается за счет использования продвинутых систем автоматизации: устройства автоматической заправки
проволоки, поиска отверстия, предотвращения обрыва проволоки, системы автоматизированной загрузки
заготовок, удаления перемычек и т. д.
Износ электрода
Эрозия при малом токе снимает мало материала заготовки, тогда как большой ток позволяет
добиться больших скоростей снятия материала.
Однако и износ инструмента возрастает, особенно при обработке стали медными электродами. Графитовые электроды
ведут себя иначе - износ до определенного момента растет, затем более или менее стабилизируется.
Короткие импульсы также приводят к ускоренному износу электрода. И наоборот, износ идет значительно медленней
при длинных импульсах. На практике, при черновой обработке стали медным и графитовым инструментом оптимальная
величина длительности импульса лежит на отрезке, на одном конце которого длительность импульса с максимальным
съемом, а на другом - длительность импульса с минимальной интенсивностью износа инструмента.
Копировально-прошивочная обработка
Впервые об электроэрозионных станках стало известно с появлением в 1955 году первой
копировально-прошивочной установки с ручным управлением. Возможности станков были значительно улучшены к
концу 70-х годов, когда применение спутников позволило значительно уменьшить время цикла и число используемых
электродов. Примерно в 1980 году была представлена первая модель станка с СNС-управлением. К этому времени
процесс копировальной прошивки уже успел претерпеть все возможные усовершенствования, и характеристики
прошивочных СNС-станков улучшались более медленными темпами по сравнению с более "молодыми" проволочно-вырезными
станками. Наиважнейшим усовершенствованием по сравнению с ранними станками с ручным управлением было не
столько само время цикла, сколько число рабочих часов, необходимых для образования заданной полости в материале.
Ранее было замечено, что в случае проволочной резки увеличение производительности и снижение производственных
затрат в большей степени достигалось благодаря скорости резания. Что касается электроэрозионной прошивки, то
соответствующие улучшения были достигнуты благодаря существенному увеличению количества часов, которые способен
работать СNС-станок в течение дня. Обе технологии много выиграли от снижения нормочасов на каждой
детали. Переход с ручного управления на числовое программное позволил станкам работать практически всю первую
смену, интенсивно во вторую и третью в безлюдном режиме. Если для станка с ручным управлением наиболее типичной
является работа в течение 6 часов, то в случае станка с СNС-управлением реально выполнимой задачей может
быть 16 часов. Хотя на многих производствах достигаются и более высокие показатели.
Цена. Ведущие производители прошивочных станков предлагают сегодня СNС-станки (без системы автоматической смены
инструмента и оси С) примерно по той же цене, по которой в середине 70-х продавались станки с ручным
управлением (инфляция учитывается). Даже если добавить стоимость необходимых опций, то скорректированная цена
такого нового станка примерно будет равна цене станка 70-х с ручным управлением, который оснащен спутником.
Любое повышение цены будет существенно перевешиваться снижением времени цикла, нормочасов и увеличением времени,
которое оборудование реально работает в течение суток.
Точность обработки. Учитывая характер процесса формообразования при электроэрозионной прошивке, точность
обработки в большей степени будет зависеть от качества и точности изготовления электрода. Графит - более дешевый
и удобнообрабатываемый материал - в сочетании с современными технологиями высокоскоростной
фрезерной обработки
позволяет получать электроды большой сложности и высокой точности.
Определенные успехи были достигнуты и в отношении плоскостности обработанных поверхностей. Например, суммарное
отклонение для прямоугольной полости 150х200 мм, полученной на современном станке, составляет всего 0,008 мм.
| |